What is a Repair Alloy Wheel Lathe?
Q: What purpose does a repair alloy wheel lathe serve?
A: A repair alloy wheel lathe is a precision machine tool specifically designed to refurbish and machine alloy wheels for vehicles like cars and motorcycles. Alloy wheels are popular for their aesthetic appeal, lightweight nature, and performance benefits, but they are also prone to scratches, deformations, and other damages from road use. A repair alloy wheel lathe restores damaged alloy wheels’ appearance and structural integrity, extending their lifespan and maintaining vehicle performance.
Choosing the Right Guide Rail for a Wheel Repair Lathe
Q: What type of guide rail should be used to repair the alloy wheel lathe?
A: Choosing between hard rail (box way) and linear rail (linear guideway) is crucial for a wheel repair lathe‘s efficiency. This decision significantly affects the lathe’s precision, speed, and longevity, which in turn determines the quality and efficiency of wheel repairs.
Hard Rail (Box Way): The Traditional Choice for Rigidity and Damping
Hard rails, known as box ways, offer a large contact area with the moving carriage, providing excellent load-bearing capacity and vibration-damping characteristics. This is particularly advantageous when the alloy wheel repair lathe handles heavy or oversized wheels, where rigidity ensures precision and consistency in cutting without deflection. Moreover, the damping properties help absorb vibrations during the machining process, protecting the lathe components, prolonging service life, and improving surface finish.
However, the downside of hard rails is their higher friction, which can lead to accelerated wear over time. They also require regular lubrication and maintenance to prevent scoring and ensure smooth operation. The increased friction often limits the speed of the carriage movement, potentially reducing the overall efficiency of the wheel repair process.
Linear Rail (Linear Guideway): The Modern Choice for Speed and Precision
Linear rails offer a more modern solution for machine tool guideways. Consisting of rolling elements such as balls or rollers, linear rails provide point contact between the carriage and the rail, significantly reducing friction, and allowing for faster movement and higher precision.
For a wheel repair machine in a repair shop, linear rails could provide quicker setup times and faster machining cycles due to their high-speed capabilities. The reduced friction also means less wear and a lower maintenance burden. Additionally, linear rails offer superior positioning accuracy and repeatability, essential for achieving the precise dimensions required in wheel repairs.
Despite these advantages, linear rails have limitations. Their point contact is not as effective at absorbing vibrations compared to the broad contact of hard rails, which may result in less stable machining processes, particularly with larger, heavier wheels. Furthermore, linear rails might not perform well under heavy loads, potentially affecting their lifespan and reliability.
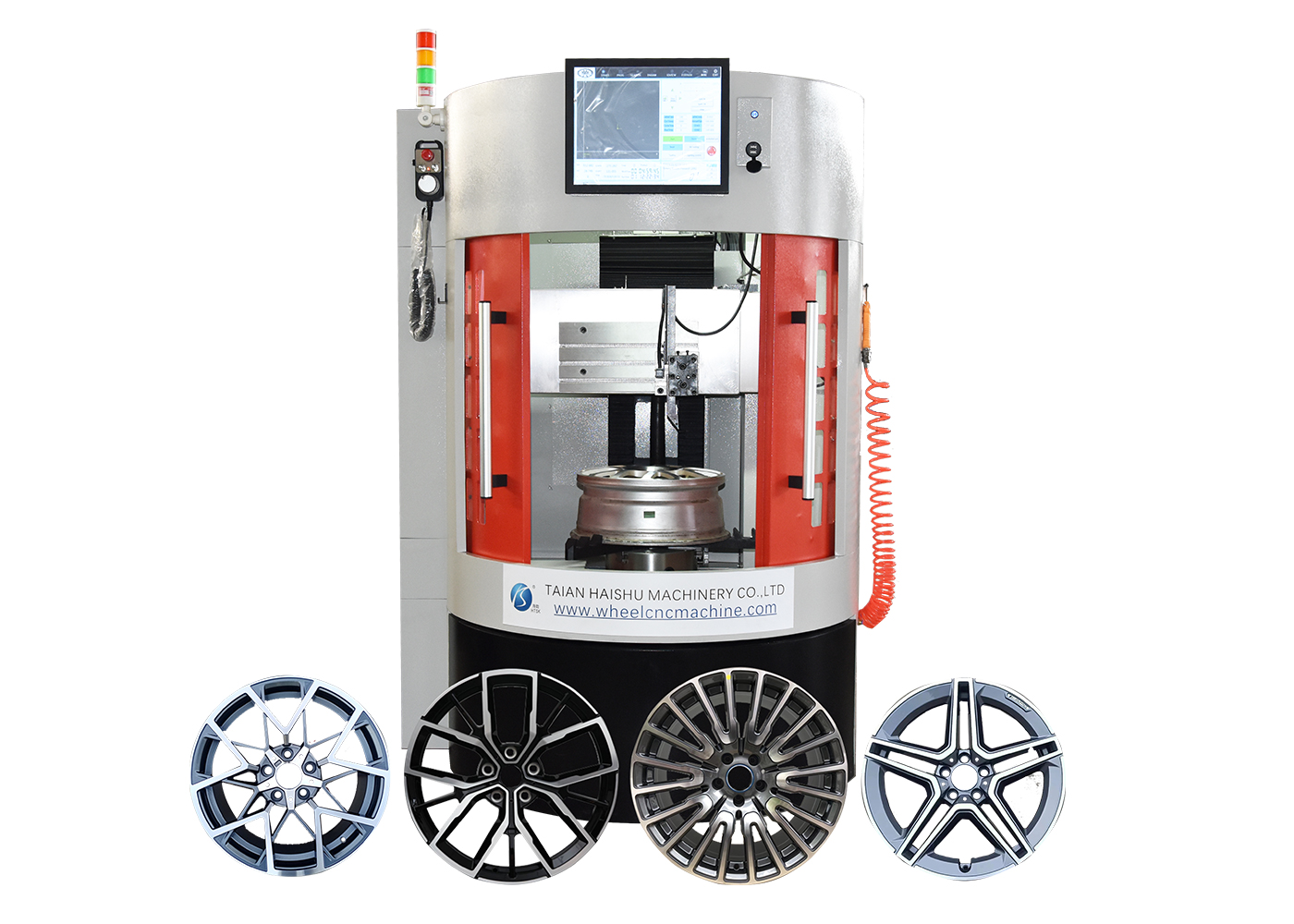
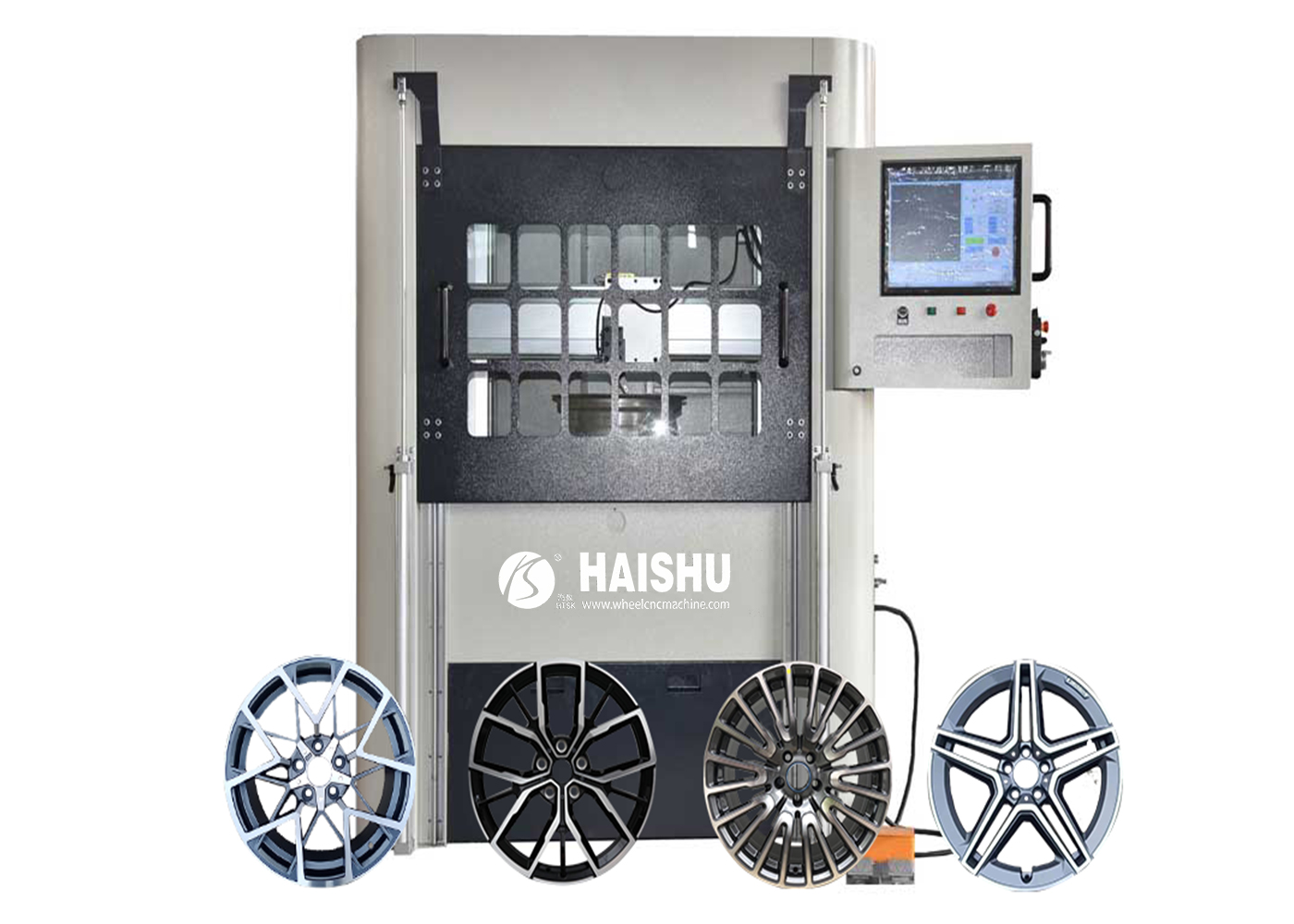
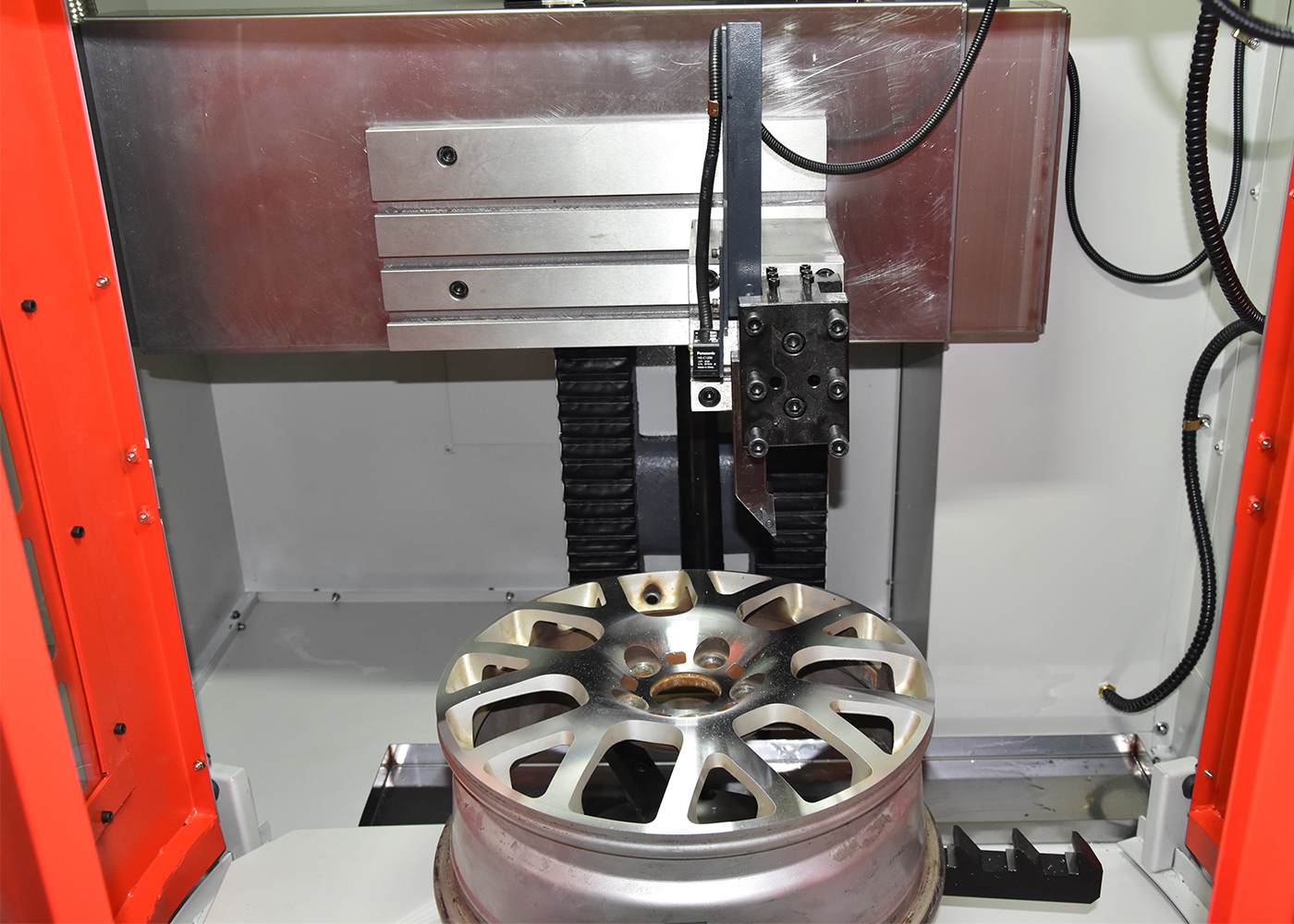
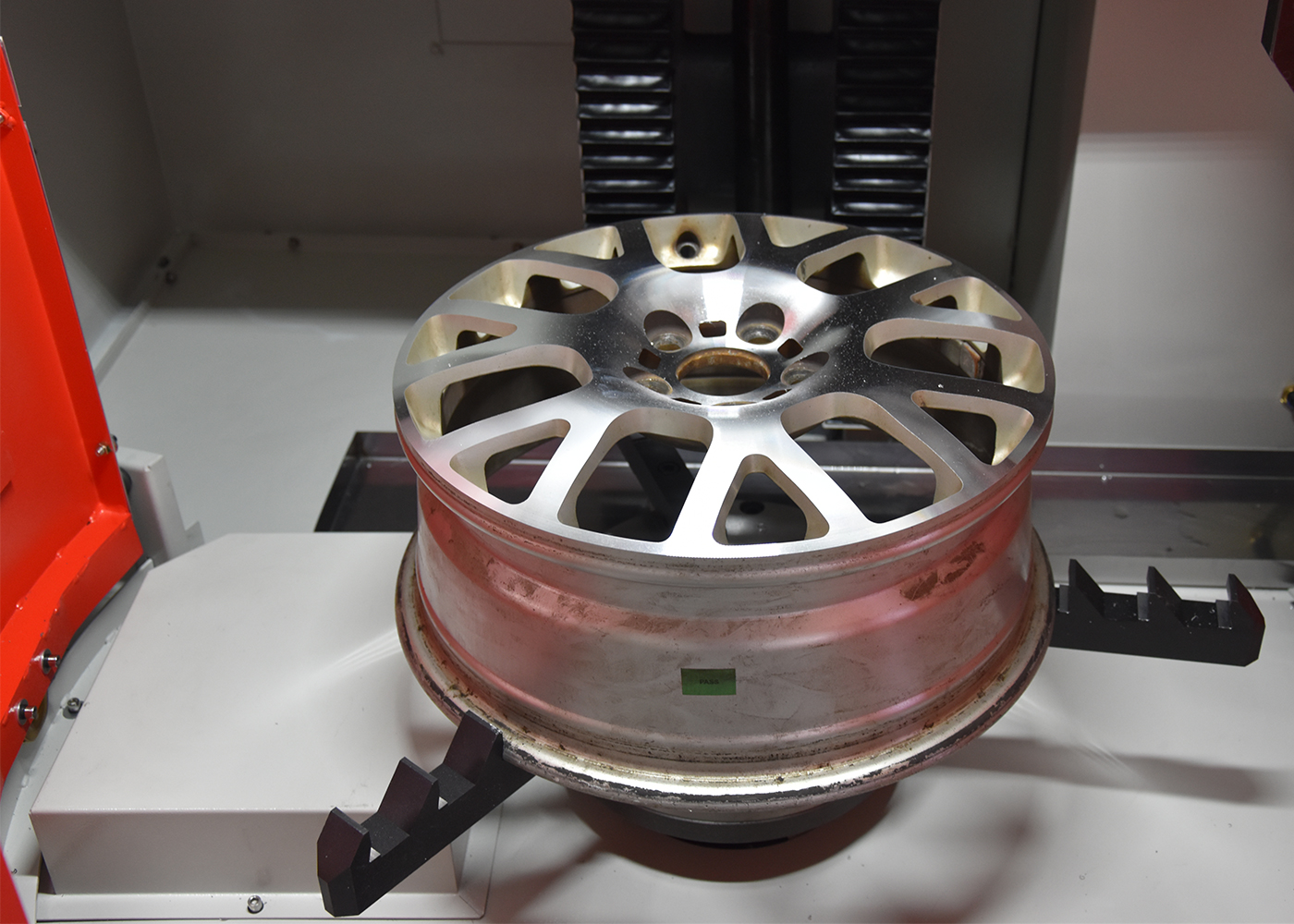
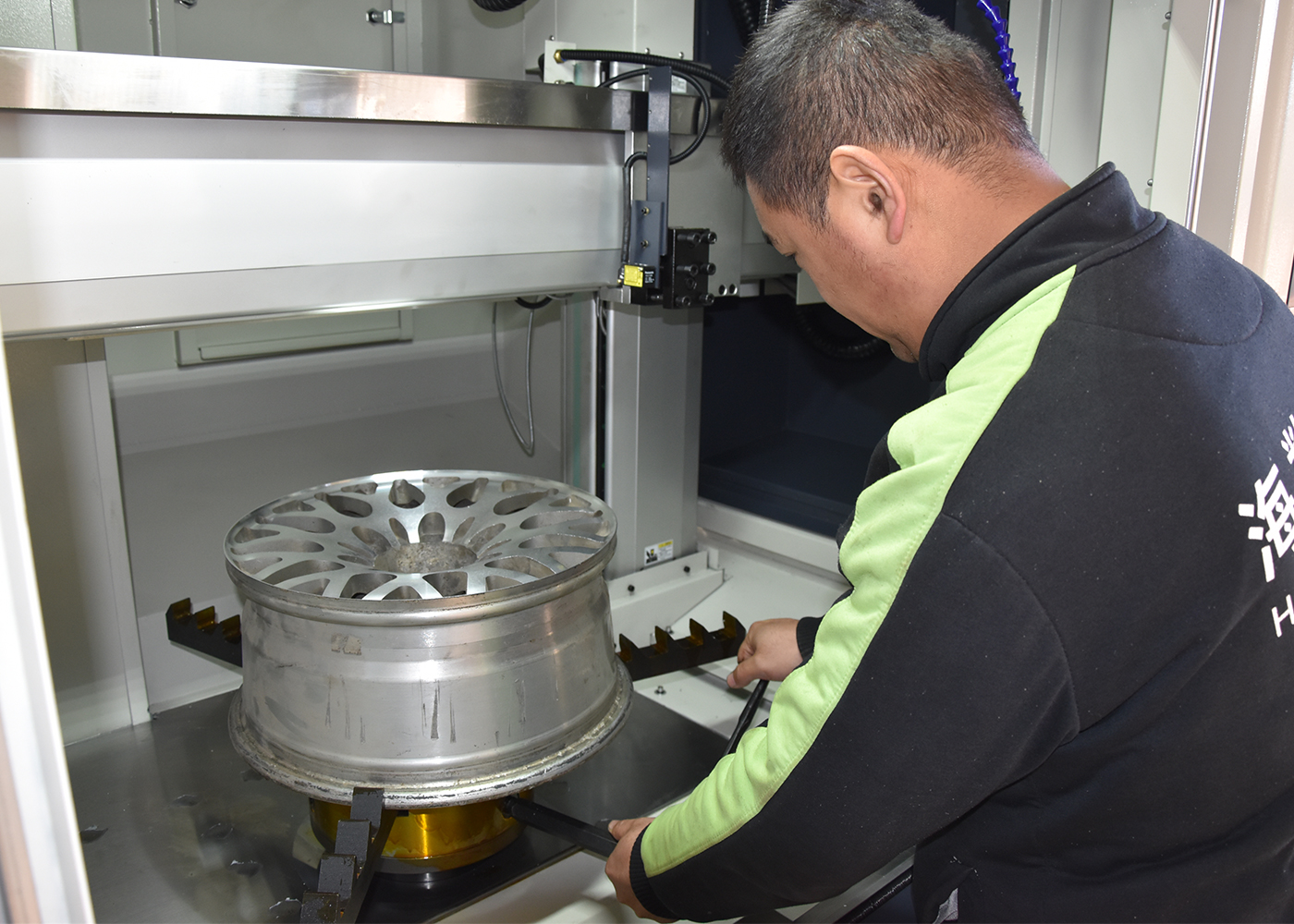
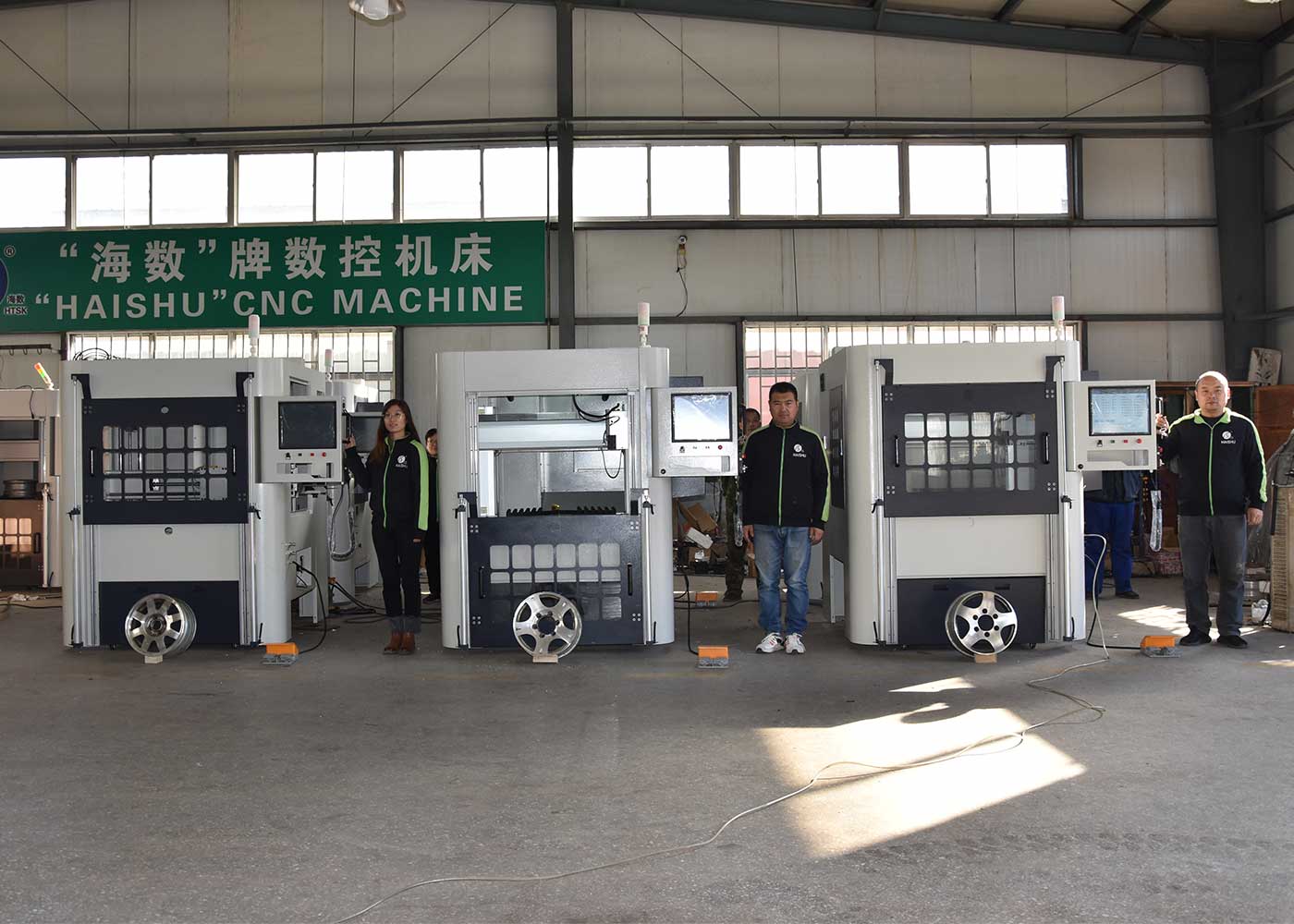
Making the Decision: Which Guide Rail is Better for a Wheel CNC Machine?
Q: How do we decide between hard rails and linear rails for a wheel CNC machine?
A: The choice between hard rails and linear rails for a wheel CNC machine depends on the specific requirements of the repair tasks. If the focus is on machining large, heavy wheels where rigidity and vibration damping are crucial, hard rails might be the preferred option. They offer the stability and robustness needed for challenging jobs.
Conversely, if the priority lies in high throughput and rapid turnaround repairs that demand speed and precision, linear rails might be the better choice. Their rapid, accurate, and low-maintenance operation can significantly enhance productivity.
Taian Haishu Machinery Co., Ltd. has developed a vertical wheel repair lathe that combines rigidity with operational efficiency. One model is the CKL35, and the other is the CKL22Q. The CKL35 features a gantry fixed beam structure, capable of repairing wheels up to 35 inches in diameter, with a dual-column gantry structure that provides extra rigidity. The spindle unit configuration ensures perfect harmony between speed and machining transmission. The CKL22Q, on the other hand, has a cast structure with enlarged and thickened linear rails, offering high-speed movement while providing substantial rigidity support. Our company’s alloy wheel repair lathes cover all automotive wheels in the market. For specific configurations and pricing, you are welcome to consult us. We look forward to your inquiries.